Food Grade Epoxy Coatings
Description:
Food grade epoxy is a type of epoxy resin that is safe for use with food and drinking water. It is often used to line and coat portable water tanks made from different materials such as reinforced cement concrete (RCC), metal, or plastic.
In the case of RCC water tanks, food grade epoxy is used to provide a protective coating on the inside of the tank, preventing the leaching of harmful chemicals or contaminants into the water. The coating also helps to improve the durability and lifespan of the tank.
Similarly, in the case of metal or plastic water tanks, food grade epoxy can be used to line the interior of the tank to prevent corrosion or chemical leaching that may occur due to the materials used in the tank. This coating provides a barrier between the water and the metal or plastic, ensuring that the water remains safe for consumption.
When selecting a food grade epoxy for portable water tanks made from different materials, it is important to choose a product that is compatible with the specific material. For example, a food grade epoxy suitable for use with RCC tanks may not be suitable for use with plastic or metal tanks.
It is also important to ensure that the food grade epoxy used meets regulatory standards for safety and quality, such as those set by the Bureau of Indian Standards (BIS). This will help to ensure that the water stored in the tank remains safe for consumption and that the tank itself does not leach any harmful substances into the water.
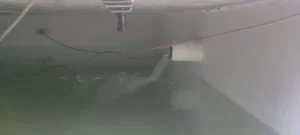
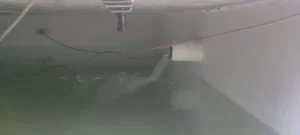
Two-component food grade epoxy is a type of epoxy coating that consists of two separate parts that must be mixed together before use. It is formulated to be safe for use in contact with food and drinking water, and is often used to coat or line equipment and surfaces in food processing and storage facilities..
Anti-microbial/anti-fungal/anti-algae properties of Food Grade Epoxy effectively prevent the growth of harmful elements that are hazardous to human beings. It is a non-toxic and Eco-friendly coating that is 100% safe for potable water contact and has been tested and certified for the same. It possesses excellent water resistance, adhesion, hardness & toughness properties similar to solvent based epoxy compositions.
Uses:
Two-component food grade epoxy coatings are suitable for use in a variety of locations where food and drink are stored or processed. Here are some examples:
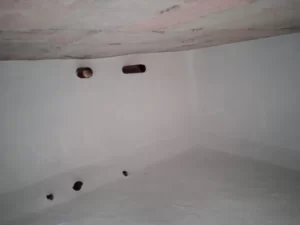
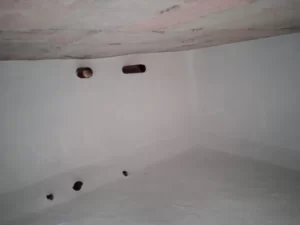
- Food processing facilities: Two-component food grade epoxy coatings can be used to coat the floors, walls, and ceilings of food processing facilities, including commercial kitchens, bakeries, and meat processing plants. The coating provides a hygienic surface that is easy to clean and sanitize, and helps to prevent contamination.
- Beverage production facilities: Two-component food grade epoxy coatings are commonly used to coat the tanks and other equipment used in beverage production facilities, such as breweries, wineries, and distilleries. The coating protects the equipment from corrosion and provides a smooth surface that is easy to clean.
- Storage tanks and vessels: Two-component food grade epoxy coatings can be used to line storage tanks and vessels used for storing water, juices, or other beverages. The coating prevents corrosion and leaching of harmful chemicals into the stored liquids, and ensures that the stored beverages remain safe for consumption. Concrete or Cement plastered water tanks.
- Retail food outlets: Two-component food grade epoxy coatings can be used to coat floors, walls, and countertops in retail food outlets, such as supermarkets and grocery stores. The coating provides a hygienic surface that is easy to clean and helps to prevent contamination.
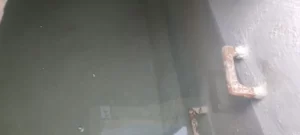
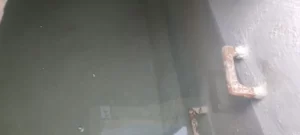
Features & Benefits
The properties you mentioned are characteristics of a type of coating or paint that has specific benefits for various applications. Here are some potential uses of a coating that possesses the following properties:
- Microbial resistance: The coating can be used to paint surfaces in hospitals, clinics, and laboratories, where microbial growth and cross-contamination are concerns. It can also be used in food processing facilities to prevent the growth of mold, fungi, and bacteria.
- Eco-friendly and Non-Toxic: The coating can be used in residential, commercial, and industrial settings where people may be exposed to the coating. For example, it can be used in schools, offices, or hospitals where there are people with respiratory sensitivities or allergies.
- Non-Hazardous and Non-Flammable: The coating can be used in areas where flammable or hazardous materials are not allowed, such as in airports, hotels, or public buildings.
- Adhesion: The coating can be used on concrete surfaces, including floors, walls, and ceilings, to provide a hard and tough film that is resistant to wear and tear. It can also be used on metal surfaces to provide an excellent adhesion.
- Application Advantage: The coating can be used on damp concrete or plaster surfaces, making it ideal for use in areas where moisture is present, such as basements, garages, and bathrooms.
- Water Permeability: The coating can be used on surfaces that are exposed to water, such as swimming pools, fountains, and water tanks, to reduce water permeability and prevent damage from water infiltration.
- Resistance: The coating can be used in areas where there is exposure to water, salt water, mild acids, alkalis, and soap water, such as in industrial settings where chemicals are present.
- Economical: The coating can be used in large areas such as parking garages or warehouses, where high coverage is required, making it an economical choice.
- Durability: The coating can provide a long-lasting and durable finish that can withstand harsh weather conditions, chemical exposure, and abrasion.
- Versatility: The coating can be used on a variety of surfaces, including concrete, metal, plastic, and wood, making it a versatile solution for many applications.
- Aesthetics: The coating can be tinted to a range of colors and finishes, including glossy, matte, or satin, to enhance the appearance of the surfaces it is applied on.
- Easy to Clean: The coating can be easily cleaned with water and mild soap, making it a low maintenance option for areas that require frequent cleaning, such as kitchens, bathrooms, and hospitals.
Application
The application procedure for food-grade epoxy will depend on the specific product being used, as different brands may have slightly different instructions. However, here are the general steps involved in applying food-grade epoxy:
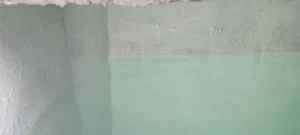
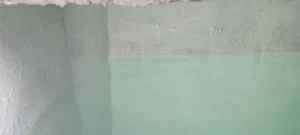
- Surface Preparation: The surface must be clean, dry, and free of dust, debris, and other contaminants. If necessary, the surface should be sandblasted, ground, or shot-blasted to achieve the correct profile. Waterproofing of RCC water tanks, Fill the cracks/ grooves with Food grade Epoxy modified putty & allow it to dry for at least 24 hours.
- Mixing: Food-grade epoxy comes in two components, a resin and a hardener, that need to be mixed thoroughly according to the manufacturer’s instructions. It is important to use the correct mixing ratio and mix the components for the recommended time.
- Application: Once the two components are mixed, the epoxy should be applied using a brush, roller, or spray. The thickness of the coating will depend on the manufacturer’s recommendations and the specific application.
- Apply the first brush coat of mixed quantity of Food grade Epoxy. Allow it to dry for 6 to 8 hours. Apply second brush coat of Food grade Epoxy. Allow it to cure for minimum 7 days prior to storage of the water. The treated surface must be cleaned well with plenty of water prior to storage of the potable water.
- Curing: Food-grade epoxy will cure over time, and the curing time will depend on the product used, as well as environmental factors such as temperature and humidity. It is important to follow the manufacturer’s instructions regarding the curing time and temperature to ensure proper curing.
GEOLIZ WATERPROOFERS PVT. LTD.
Waterproofing Products & Services Guide
For details on other waterproofing products & Services